обозначение опор, зажимов и установочные устройств
На технологических эскизах эти обозначения служат указателями баз, а важность базирования переоценить трудно. Поэтому, прежде чем перейти к понятию баз и базирования в машиностроении, мы рассмотрим, как в технологической документации изображают опоры, зажимы и установочные устройства согласно ГОСТ 3.1107-81.
Обратите внимание, для изображения обозначения опор, зажимов и установочных устройств следует применять сплошную тонкую линию по ГОСТ 2.303-68.
Условные обозначения опор приведены в таблице 1.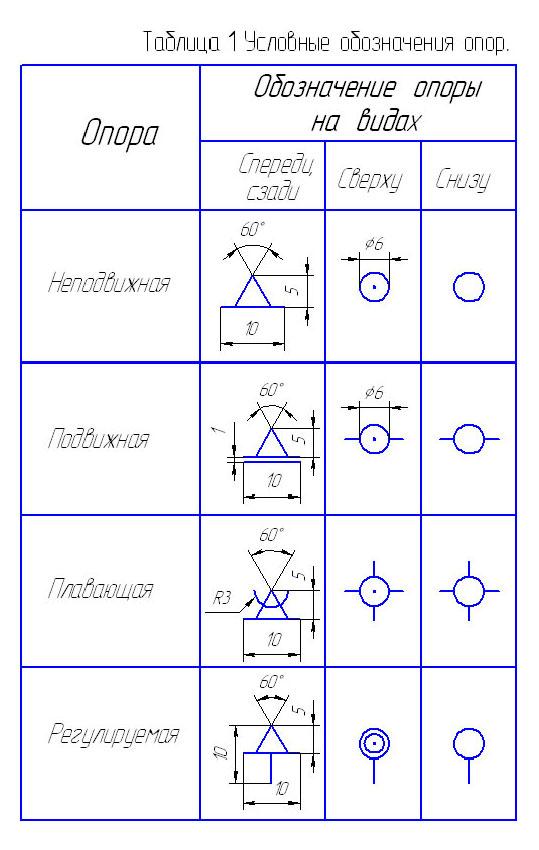
Несколько обозначений одноименных опор на схемах на каждом виде допускается заменять одним с обозначением их числа справа. Кроме того допускается обозначение подвижной, плавающей и регулируемой опор на видах сверху и снизу изображать как обозначение неподвижной опоры на аналогичных видах.
В качестве примера можно привести вал, установленный в трехкулачковом патроне, с упором в торец и с креплением в подвижном люнете.
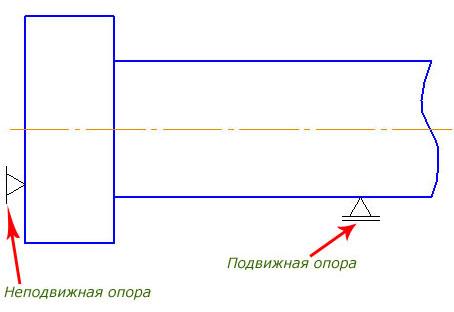
Условные обозначения зажимов приведены в таблице 2.
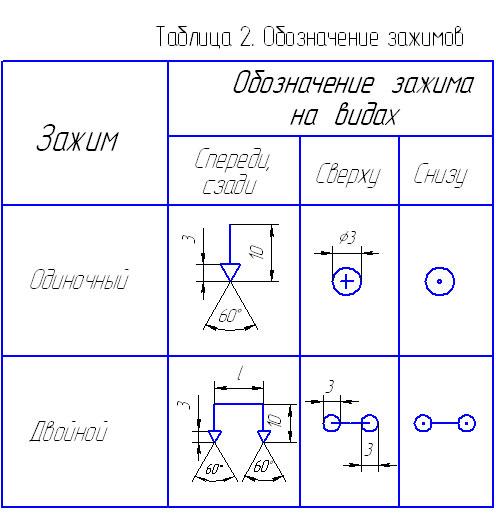
Количество точек приложения сил зажима к изделию, записывается справа от обозначения зажима.
Для двойных зажимов длина плеча устанавливается разработчиком в зависимости от расстояния между точками приложения сил. Допускается упрощенное графическое обозначение двойного зажима:
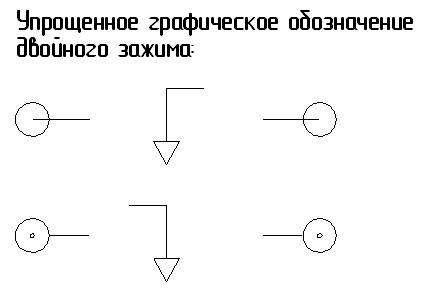
Обозначение двойного зажима на виде спереди или сзади при совпадении точек приложения сил допускается изображать как обозначение одиночного зажима на аналогичных видах.
В качестве примера обозначения зажимов можно привести деталь, установленную в кондукторе, с упором на три неподвижных опоры, и с применением устройства (электрического, пневматического) двойного зажима.
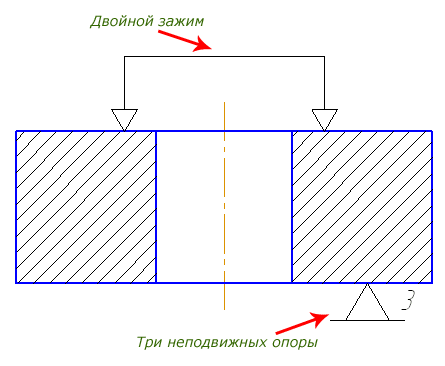
Условные обозначения установочных устройств приведены в таблице 3.
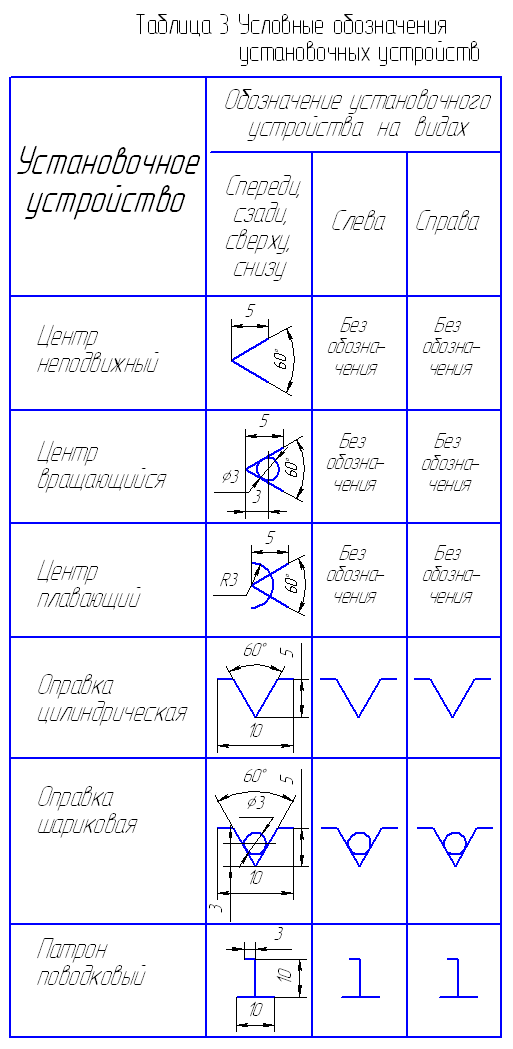
Если устройство установочно-зажимное то его обозначают сочетанием обозначений зажимов и установочных устройств.
Обозначение опор и установочных устройств, за исключением центров, допускается наносить на выносные линии соответствующих поверхностей.
Обратные центра выполняются в зеркальном изображении.
Цанговые оправки (патроны) следует обозначать
Для базовых установочных поверхностей допустимо применять обозначение
В качестве примера обозначения установочных устройств, можно привести деталь установленную в цанговом патроне с механическим устройством зажима, с упором в торец, с поджимом вращающемся центром и с креплением в подвижном люнете.
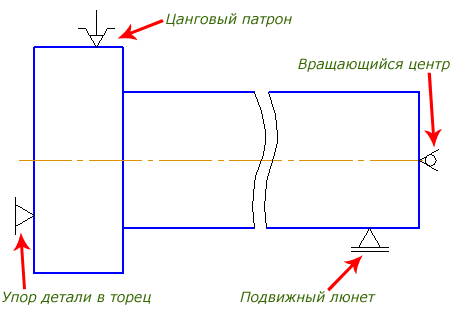
Обозначения форм рабочей поверхности опор, зажимов и установочных устройств приведены в таблице 4.
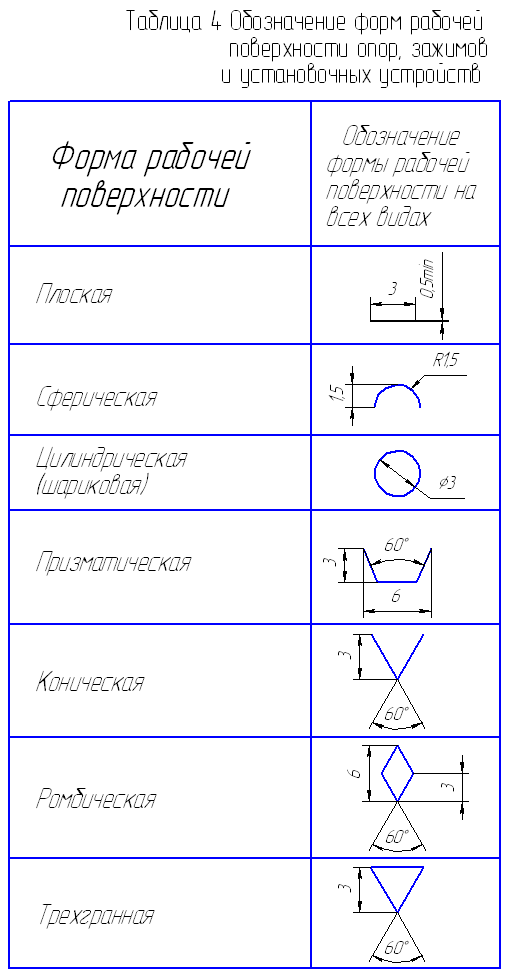
Рифленая, резьбовая, шлицевая и т.д. поверхности опор, зажимов и установочных устройств обозначаются в соответствии с чертежом.
Обозначение форм рабочих поверхностей следует наносить слева от обозначения опоры, зажима или установочного устройства.
Для указания устройств зажимов следует применять обозначения в соответствии с таблицей 5.
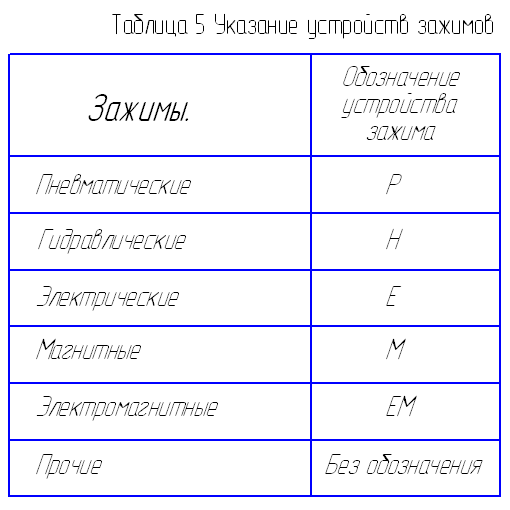
Обозначение видов устройств зажимов наносят слева от обозначения зажимов.
В качестве примера обозначения форм рабочей поверхности опор, зажимов и установочных устройств, можно привести деталь которая закрепляется при помощи пневматического зажима, с цилиндрической рифленой рабочей поверхностью.
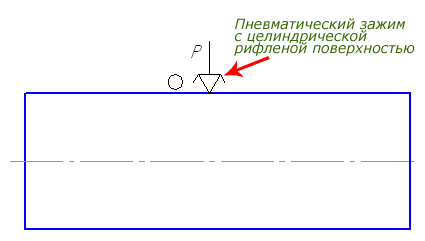
Если схема имеет несколько проекций, допускается на отдельных проекциях не указывать обозначения опор, зажимов и установочных устройств относительно изделия, если их положение однозначно определяется на одной проекции.
И в заключение, инженеру-технологу следует иметь ввиду, что допускаются отклонения от размеров графических обозначений, указанных в таблицах 1-4.
В этой статье мы рассмотрели обозначение опор, зажимов и установочных устройств. В следующих статьях поговорим о понятии баз и базировании заготовок в машиностроении.
Основы теории базирования.

Термины и определения основных понятий базирования и баз регламентируютсяГОСТ 21495-76.
Базирование – придание заготовке или изделию требуемого положения относительно выбранной системы координат.
База – поверхность или выполняющее ту же функцию сочетание поверхностей, ось, точка, принадлежащая заготовке или изделию и используемая для базирования.
Твердое тело может быть неподвижным, т.е. занимать постоянное неизменное положение в данной системе координат, или может передвигаться, изменять свое положение относительно определенной системы координат. Постоянное положение или движение тела достигается наложением геометрических или кинематических связей.
Условие, ограничивающее перемещение, называется геометрической связью.
Условие, ограничивающее скорость перемещения, называется кинематической связью.
Геометрические связи бывают односторонние и двусторонние.
В качестве примера двусторонней связи рассмотрим шар, находящийся между двумя параллельными плоскостями, расстояние между которыми равно диаметру шара. Плоскости ограничивают перемещение шара вдоль оси, проходящей перпендикулярно к этим плоскостям. Двустороннюю связь можно выразить уравнением:
ZC = r, или ZC – r = 0;
где ZC – координата центра шара;
r – радиус шара.
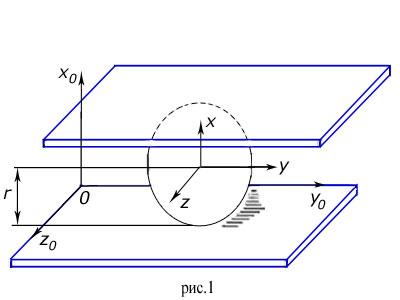
При односторонней геометрической связи движение шара в направлении координатной оси не ограничивается плоскостью, и его положение не определяется однозначно. Одностороннюю связь можно выразить неравенством:
ZC ≥ r, или ZC – r ≥ 0
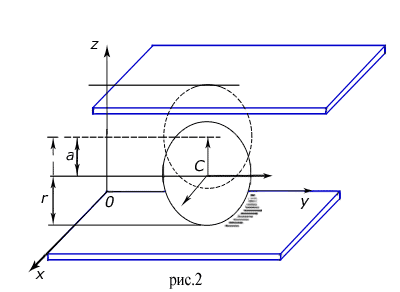
Однозначная область положения шара по оси может определяться двумя параллельными плоскостями, удаленными друг от друга на расстояние 2r + а. Тогда геометрические связи наложенные на шар выражаются двумя неравенствами:
r ≤ ZC ≤ (r + a);
т.е. двумя односторонними геометрическими связями. Если в этом выражении соблюдается знак равенства, то односторонняя связь исключает движение шара по нормали к плоскости.
Положение механической системы с наложенными геометрическими и кинематическими связями в пространстве определяется обобщенными координатами системы.
Обобщенными координатами называются независимые параметры, определяющие положение или движение механической системы в пространстве.
Координата ZC по оси Z является обобщенной координатой шара. Числом обобщенных координат выражается число степеней свободы механической системы.
Свободное твердое тело (не имеющее геометрических и кинематических связей) обладает шестью степенями свободы. Оно может перемещаться вдоль координатных осей и вращаться вокруг этих осей.
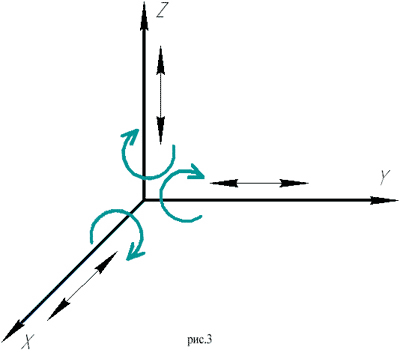
С точки зрения теоретической механики базирование заключается в придании телу определенного положения путем конечного перемещения его из произвольного положения в положение заданное двусторонними геометрическими связями, выраженными размерами или координатами.
Для полной определенности положения твердого тела в пространстве необходимо и достаточно наложить на точки тела шесть двусторонних геометрических связей и тем самым лишить его шести степеней свободы.
Опорная точка – точка, символизирующая одну из связей заготовки или изделия с выбранной системой координат.
При базировании заготовки или изделия в выбранной системе координат, чтобы лишить тело степеней свободы на него необходимо наложить двусторонние геометрические связи. Необходимое и достаточное условие для базирования твердого тела наложение на него не более шести двусторонних связей.
Правило шести точек – создание шести опорных точек при базировании.
Если по служебному назначению изделие имеет определенное число степеней свободы, то соответствующее количество связей не накладывается. Если требуется обеспечить движение, то накладываются соответствующие кинематические связи.
Для формирования системы координат необходим комплект баз.
Комплект баз – совокупность трех баз, образующих систему координат заготовки или изделия.
На базах комплекта обозначаются опорные точки, символизирующие связи с выбранной системой координат, таким образом создается схема базирования.
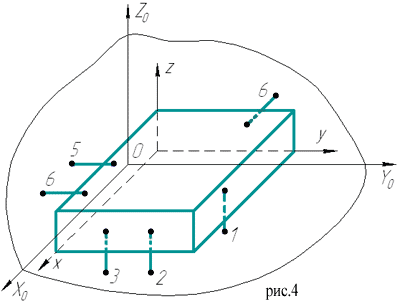
Схема базирования – схема расположения опорных точек на базах.
Опорные точки на схеме базирования изображают условными значками и пронумеровывают порядковыми номерами, начиная с базы имеющей наибольшее количество опорных точек. Если в какой либо проекции одна опорная точка накладывается на другую, изображается одна точка, и проставляются номера совмещенных точек. Число проекций на схеме базирования должно быть достаточным для четкого представления о размещении опорных точек. Схема базирования для твердого тела рис. 4 представлена на рис. 5.
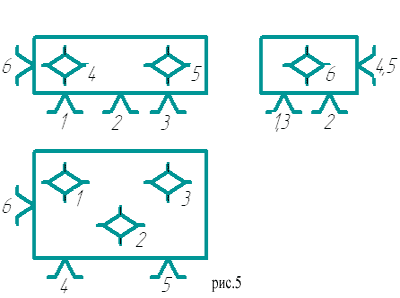
Кроме баз, заготовки и изделия имеют множество других конструктивных элементов, положения этих элементов могут быть заданы в различных системах координат базируемых тел. Соответственно положение точек, линий и поверхностей, заданных в различных системах координат базируемого тела, определяют расчетом размерных цепей. Если в системе координат базируемого тела заданы координаты его формообразующих точек, линий и поверхностей, то положение этих элементов относительно внешней системы координат необходимо определять суммированием координат, которые образуют размерную цепь конструктивных элементов базируемой заготовки или изделия.
В процессе базирования необходимо наложить требуемые двусторонние связи. Их можно обеспечить геометрическим замыканием (базирование вала в отверстии), либо закреплением.
Закрепление – приложение сил и пар сил к заготовке или изделию, для обеспечения постоянного их положения, достигнутого при базировании.
В производственной практике часто выполняется закрепление без базирования, без придания требуемого положения.
Понятие установки определяет отличие процесса базирования и закрепления заготовок от закрепления без базирования.
Установка – базирование и закрепление заготовки или изделия.
Базирование и закрепление могут осуществляться отдельно или одновременно, например с использованием самоцентрирующих зажимов (патроны, цанги, разжимные оправки).
В технологической документации на операционных эскизах изображаются схемы установки с использованием соответствующих обозначений опор, зажимов и установочных устройств по ГОСТ 3.1107-81.
В следующей статье рассмотрим класификацию баз.
Базирование. Классификация баз.

Базы принято классифицировать по назначению, по лишаемым степеням свободы и по способу их проявления.
Классификация баз по назначению.
По назначению базы подразделяются на:
Конструкторские;
Технологические;
Измерительные.
Конструкторская база – база, используемая для определения положения детали или сборочной единицы в изделии. Они подразделяются на основные и вспомогательные.
Основная база – конструкторская база детали или сборочной единицы, используемая для определения их положения в изделии.
Вспомогательная база – конструкторская база детали или сборочной единицы, используемая для определения присоединяемого к ним изделия.

Технологические базы назначают при технологическом проектировании изготовления изделий и непосредственно в процессе их производства.
Технологическая база – база, используемая для определения положения заготовки или изделия при изготовлении и ремонте.
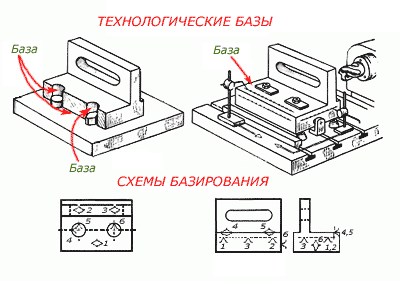
При контроле размеров, точности формы и расположения поверхностей выполняются измерения с использованием измерительных баз.
Измерительная база – база, используемая для определения относительного положения заготовки или изделия и средств измерения.

В машиностроении существует четыре вида поверхностей деталей и изделий:
исполнительные поверхности, с их помощью деталь выполняет свое служебное назначение;
основные поверхности, с их помощью определяется положение данной детали в изделии;
вспомогательные поверхности, с их помощью определяется положение присоединяемых деталей относительно данной;
свободные поверхности, не соприкасающиеся с поверхностями других деталей.
Обратите особое внимание, базирование необходимо на всех стадиях создания изделия: конструирование, изготовление и измерения. Кроме того, теория базирования распространяется на все технологические системы, и не только изделия, но и заготовки могут иметь не один комплект баз.
Деление технологических баз на основные и вспомогательные стандартами не предусмотрено, но все же необходимо их различать. В технической литературе и в практике существует понятие – настроечная технологическая база. Настроечная технологическая база – база, относительно которой базируется инструмент при настройке, и по отношению к которой с помощью инструмента формируются обрабатываемые поверхности, связанные с настроечной базой непосредственными размерами требуемого положения.
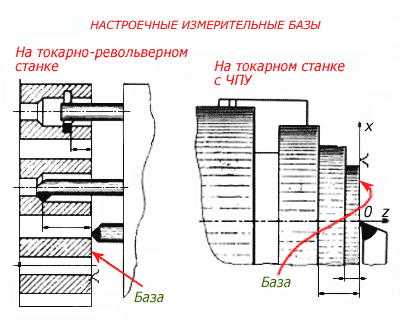
При разработке технологической документации, решая вопрос базирования и настройки инструментов в технологической системе, рекомендуется в качестве баз использовать конструкторские базы. Это обеспечивает сокращение размерных цепей и соответственно позволяет повысить точность изготовления изделий.
Одним из важнейших элементов технологического процесса изготовления или ремонта изделий являются контрольно-измерительные операции. Часто измерения составляют неразрывную часть технологических операций изготовления изделий и реализуются на одном рабочем месте при обработке заготовок, наладке или сборке. В качестве примера можно привести базирование инструментальных блоков или рабочих органов оборудования с числовым программным управлением относительно выбранной системы координат станка (изделия) или заготовки. Другими словами с помощью средств измерений осуществляется проверка, выверка и придание требуемых положений элементам изделий или технологических систем, включая заготовки и изделия технологической оснастки.
Существует еще один термин, который Вы не встретите в стандарте, но можете повстречать в справочной литературе это проверочные технологические базы.
Проверочные технологические базы используются для базирования и проверки требуемого положения при изготовлении изделия. Их можно определить и как измерительные, поскольку положение этих баз проверяется визуально или с помощью средств измерения.
Обратите внимание, базируя инструмент при наладке, фактическую погрешность базирования относят к погрешности настройки.
Кроме классификации приведенной выше, в производственной практике и литературе различают также искусственные, черновые и чистовые технологические базы.
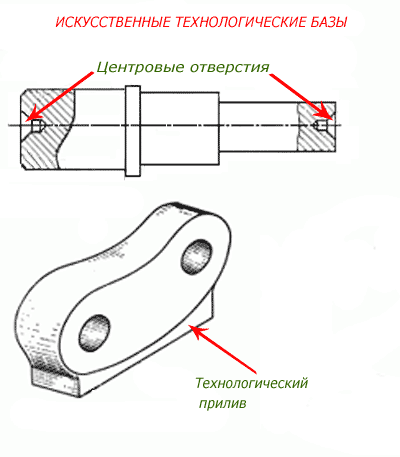
Искусственная технологическая база – база, которая как конструктивный элемент не требуется для готового изделия, а также база, которая в целях повышения точности базирования обрабатывается с более высокой точностью, чем требуется по служебному назначению. Лучший пример искусственных баз, центровые отверстия вала, их используют для установки при изготовлении изделия.
Выбор баз зависит не от стадии производства, а от характеристики размеров, формы, шероховатости и точности конструктивных элементов на разных этапах производства. Поэтому различают выбор баз из черновых (необработанных) элементов заготовки и из чистовых (обработанных) элементов заготовки.
Черновой технологической базой называют базу, используемую при выполнении первого установа после получения заготовки. Их назначение в том, чтобы обработать и подготовить чистовые (обработанные и более точные) базы для выполнения последующих операций изготовления изделия. Поскольку точность необработанных баз всегда ниже точности обработанных (чистовых) баз, а шероховатость выше, то черновые базы при обработке заготовки должны использоваться только один раз – при выполнении первого установа или при изготовлении изделия с одной установки. При смене баз необходимо использовать чистовые (обработанные), точные базы.
Смена баз – замена одних баз другими с сохранением их принадлежности к конструкторским, технологическим или измерительным.
В следующей статье рассмотрим классификацию баз по лишаемым степеням свободы и по способу проявления.
Базирование. Классификация баз.

Классификация баз по лишаемым степеням свободы.
Классификация баз по лишаемым степеням свободы делается на основе анализа способов базирования тел с учетом отличительных признаков геометрической характеристики их элементов (точек, линий, осей, поверхностей и их сочетаний), образующих материальные и геометрические тела, заготовки и изделия, базы и системы координат.
Введем несколько новых понятий, а затем рассмотрим каждое из них.
Установочная база – база, используемая для наложения на заготовку или изделие связей, лишающих их трех степеней свободы – перемещения вдоль одной координатной оси и поворотов вокруг двух других осей.
Направляющая база - база, используемая для наложения на заготовку изделие связей, лишающих их двух степеней свободы – перемещения вдоль одной координатной оси и поворота вокруг другой оси.
Опорная база – база, используемая для наложения на заготовку или изделие связей, лишающих их одной степени свободы – перемещения вдоль одной координатной оси или поворота вокруг оси.
Для того чтобы полностью определить положение тела в пространстве необходимо лишить его шести степеней свободы: трех поступательных перемещений вдоль осей координат, и трех вращательных вокруг этих осей.
Если нижнюю поверхность призматического тела соединить тремя жесткими двусторонними связями 1, 2 и 3 с тремя точками , плоскости XOY выбранной системы координат, не лежащими на одной прямой, тело приобретет устойчивое положение и лишится трех степеней свободы. Данное тело не сможет перемещаться вдоль оси Z и вращаться вокруг осей X и Y. Такая база называется установочной, смотри рисунок ниже.
Если связать боковую поверхность призматического тела двумя жесткими двусторонними связями 4 и 5 с двумя точками плоскости XOZ, тело лишится еще двух степеней свободы. Оно не сможет перемещаться вдоль оси Y и вращаться вокруг оси Z. Такая база называется направляющей, смотри рисунок ниже.
Чтобы добиться полного базирования данного тела необходимо лишить его шестой степени свободы. Для этого соединяем вторую боковую поверхность одной жесткой двусторонней связью 6 с точкой плоскости YOZ, тем самым лишая тело возможности перемещения вдоль оси Х. Такая база называется опорной, смотри рисунок ниже.
Само собой обязательно наличие силового замыкания.
Базирование длинных цилиндрических тел (LD).
Для базирования длинных цилиндрических тел используется двойная направляющая база. Цилиндрическая поверхность соединяется двумя связями 1, 2 с плоскостью XOZ и двумя связями 3, 4 с плоскостью XOY, тем самым лишая тело четырех степеней свободы – возможности перемещения вдоль осей Y и Z, а также поворотов вокруг этих осей.
Двойная направляющая база – база, используемая для наложения на заготовку или изделие связей, лишающих их четырех степеней свободы – перемещений вдоль двух координатных осей и поворотов вокруг этих осей.
Соединение торца двусторонней связью 5 с плоскостью YOZ, лишит тело возможности перемещения вдоль оси Х. Данная база, будет являться опорной.
Чтобы лишить цилиндрическое тело последней, шестой степени свободы, должна быть предусмотрена еще одна двухсторонняя связь. Шестую опорную точку нужно располагать на поверхности, например шпоночной канавки, данная база будет также опорной.
Ниже приведена схема базирования длинного цилиндрического тела
Базирование коротких цилиндрических тел (L
Сначала лишим тело трех степеней свободы – возможности перемещаться вдоль оси Х и вращаться вокруг осей Y и Z. Для этого торцевую поверхность соединим тремя двусторонними связями 1, 2, 3 с плоскостью YOZ. По определению, приведенному ранее, эта поверхность является установочной базой.
Чтобы лишить тело возможности перемещаться вдоль осей Y и Z необходимо соединить его цилиндрическую поверхность двумя двусторонними связями 4, 5 с плоскостями XOY и XOZ. Такая база называется двойной опорной.
Двойная опорная база – база, используемая для наложения на заготовку или изделие связей лишающих его двух степеней свободы – перемещения вдоль двух координатных осей.
Чтобы лишить тело возможности поворачиваться вокруг собственной оси, нужно лишить его шестой степени свободы, это делается с помощью поверхностей шпоночной канавки. Эта поверхность будет являться опорной базой.
Комплект баз определяющих положение коротких цилиндрических тел включает в себя установочную двойную опорную и опорную базы.
Базирование конических, сферических и фасонных тел.
На базировании конических тел останавливаться подробно не будем, оно аналогично базированию цилиндрических тел. Для исключения поворота вокруг оси конус должен иметь дополнительный элемент, как и цилиндр (риску, стопорное отверстие или шпоночный паз).
Для базирования сферических тел используют сферическую поверхность её центр и оси симметрии. Чтобы обеспечить устойчивое положение шара при базировании в прямоугольной системе координат необходимо наложить три связи на три точки сферической поверхности, к примеру, базированием в упор с плоскостями выбранной системы координат. В этом случае три точки будут являться тремя опорными базами, которые лишают тело трех степеней свободы – перемещений вдоль координатных осей.
Если шар базируется с использованием центра (самоцентрирующее приспособление с двумя обратными конусами), он также лишается трех степеней свободы. В этом случае функцию опорных баз выполняет центр шара. Как и в случае с цилиндром, для полного базирования шара необходимы дополнительные элементы (метки, риски или пазы), тогда появляется возможность наложить дополнительные связи, которые лишат шар оставшихся трех степеней свободы (трех поворотов вокруг осей координат). Любое фасонное тело можно представить сочетанием геометрических элементов рассмотренных выше. Эти элементы будут выполнять функцию баз и в комплекте образовывать системы координат, используемые для базирования заготовок или изделий.
Классификация баз по способу их проявления
По характеру проявления базы разделяют на явные и скрытые.
Скрытая база – база заготовки или изделия в виде воображаемой плоскости, оси или точки.
Явная база – база заготовки или изделия в виде реальной поверхности, разметочной риски или точки пересечения рисок.
В заключение следует сказать, что согласно ГОСТ 21495-76, полные и краткие наименования баз должны состоять из частей стандартизованных терминов видов баз, располагаемых в следующем порядке: по назначению; по лишаемым степеням свободы; по характеру проявления. Например, полное наименование – «основная установочная явная база», краткое наименование – «измерительная явная база»; «технологическая база».
Базирование.
Основные формулы для расчета погрешностей базирования и закрепления заготовки.

Отклонения от геометрической формы и размеров, возникающие в процессе обработки заготовки, должны находиться в пределах допусков, определяющих максимально допустимые значения погрешностей размеров и формы детали. При механической обработке обеспечение заданной точности зависит от выбора технологических баз и схемы установки заготовок.
Погрешность установки заготовки можно рассчитать по формуле:
где,
ΕБ - погрешность базирования;
ΕЗ - погрешность закрепления;
ΕП.З - погрешность положения заготовки.
где,
ΕУС - погрешность вызванная неточностью изготовления и сборки установочных элементов приспособления;
ΕИ - погрешность вызванная износом установочных элементов приспособления;
ΕС - погрешность установки приспособления на станке.
Погрешность базирования возникает в результате базирования заготовки в приспособлении по технологическим базам, не связанным с измерительными базами. При базировании по конструкторской основной базе, являющейся и технологической базой, погрешность базирования не возникает. Погрешность закрепления образуется из поверхностей, возникающих до приложения силы зажатия и при зажатии. При работе на предварительно настроенных станках режущий инструмент, а также упоры и копиры устанавливают на размер от установочных поверхностей приспособления до приложения нагрузки, поэтому сдвиг установочных баз приводит к погрешностям закрепления. Погрешности закрепления можно определять расчетным и опытным путем для каждого конкретного способа закрепления заготовки.
Допуск выполнения заданных размеров l может быть определен как.

где,
ω - средняя экономическая точность обработки на металлообрабатывающих станках;
Для принятых методов обработки и схемы установки заготовки расчетное значение допуска Tl должно быть меньше заданного [Tl]:

Для расчета ожидаемой точности инженер-технолог должен определить:
погрешности базирования в зависимости от принятой схемы установки заготовки в приспособлении;
погрешности закрепления в зависимости от непостоянства сил зажима, неоднородности шероховатости и волнистости поверхностей заготовок, износа установочных элементов приспособлений;
погрешности вызываемые износом установочных элементов ΕИ
исполнительные размеры установочных элементов, обеспечивающие заданную точность обработки и возможность установки заготовок.
Один из важнейших факторов обеспечивающих точность изготовления деталей является точность приспособления. В процессе работы изнашиваются их установочные и направляющие элементы, и приспособление теряет требуемую точность.
Линейный износ (u) установочных элементов приспособления (опор) определяет погрешность ΕИ
Для опор: ΕИ=u
Для призм:
где,
α - угол призмы.
Величину u можно определить по формуле
где,
N - число установленных заготовок;
KУ - коэффициент, учитывающий условия обработки;
L - длина пути скольжения заготовки по опорам при досылке её до упора, мм (из условий эксплуатации приспособления);
tm - машинное время обработки заготовки в приспособлении, мин;
m, m1, m2 - коэффициенты;
Пl - критерий износостойкости;
Q - нагрузка на опору, Н;
F - площадь касания опоры с базовой поверхностью заготовки, мм2;
HV - твердость материала;
Рекомендации по выбору m, m1, m2, Пl, F, HV можно найти в справочнике под редакцией Б.Н. Вердашкина и др. «Станочные приспособления».
Допустимая величина износа [u] определяется допустимой величиной погрешности[ΕИ]
Для опор:[u]= [ΕИ]
Для призм:
Величина [ΕИ] в предположении что погрешности ΕУС и ΕС можно компенсировать настройкой станка, определяется как
При установке заготовок на отверстие с гарантированным зазором погрешность базирования является основной составляющей погрешности установки и обуславливается величиной зазора между технологической базой и установочным элементом. Максимально возможное значение зазора определяют по уравнению:
где,
TD - допуск базового отверстия заготовки (или центрирующей втулки);
Smin - минимальный зазор в сопряжении;
Td - допуск на размер установочного элемента (или базовой поверхности заготовки).
Это основные формулы для расчета погрешности базирования и закрепления заготовки. В следующей статье перейдем к практике и рассмотрим расчет погрешностей базирования и закрепления на примерах.
Базирование.
Примеры расчета погрешности базирования и закрепления заготовки.

Основные формулы для расчета погрешности базирования и закрепления заготовки были приведены в предыдущей статье. Теперь рассмотрим несколько примеров.
Пример 1.
Деталь втулка устанавливается на цилиндрический палец с буртом. Необходимо обработать ступенчатую поверхность на вертикально-фрезерном станке. Диаметр базового отверстия D=30+0,039 мм, диаметр установочного пальца d=30(-0,007-0,016) мм. Требуется определить ожидаемую точность размеров А1 и А2 (смотри эскиз ниже), если известно, что составляющие погрешности установки (погрешности закрепления и положения заготовки) равны нулю, т. е. EЗ= EП.З=0. Точность метода обработки принимается равной ω=0,120 мм(Косилова А.Г., Мещеряков Р.К, Калинин М.А. «Точность обработки заготовки и припуски в машиностроении»).
Решение:
Как видно из эскиза, заготовка устанавливается на отверстие. При такой схеме установки погрешность базирования размера А1 определяется по уравнению:
0,039+0,007+0,09=0,055 мм
Погрешность базирования при выполнении размера А2 равна нулю поскольку измерительная и технологическая базы совмещены.
Зная, что EЗ= EП.З=0, определим ожидаемую точность выполнения размеров А1 и А2 по уравнению:
0,055+0,120=0,175 мм
0+0,120=0,120
Далее, нам останется сравнить расчетное значение допуска с заданным. Должны выполняться условия:
Пример 2.
Материал заготовки чугун, шероховатость Rmax=200…300 мкм, твердость НВ 170…190. Заготовка устанавливается на рифленые опоры 7034-0379 ГОСТ 13442-68 (D= 20 мм, t=2 мм, b=0,5 мм). Сила действующая на одну опору по нормалиQ=2000±300 Н. Допустимый износ опоры [u]=300 мкм. Необходимо определить погрешность закрепления EЗ при наибольшем износе опор приспособления.
Формулы для расчета погрешности закрепления возьмем из справочника под редакцией Б.Н. Вердашкина «Станочные приспособления» (стр. 530, таблица 11).
Определяем погрешность закрепления вследствие непостоянства силы закрепления(ΔQ=600 Н) по формуле:
Определяем погрешность закрепления вследствие неоднородности шероховатости базы заготовки (ΔRmax=100 мкм) по формуле:
Определяем погрешность закрепления вследствие износа опорной поверхности установочных элементов приспособления по формуле:
Суммарная погрешность закрепления будет равна:
Пример 3
Необходимо определить исполнительный размер центрирующей втулки при установке заготовки плоской поверхностью и наружной цилиндрической поверхностью при обработке паза и выполнении размеров А1=50±0,095 мм и А2=75-0,190 мм. Технологической базой является наружная цилиндрическая поверхность, обработанная в размер d=100h8(-0,054) мм. Погрешность положения заготовки EПР, вызываемая износом центрирующей втулки EИ и погрешностью установки приспособления на станке EC, принимаем равной EПЗ=0,040 мм(Корсаков В.С. «Основы конструирования приспособлений»). Точность чернового фрезерования ω=0,060 мм.
Как показывает анализ схемы установки, точность выполнения размера А1, заданного от оси заготовки до обрабатываемой поверхности, будет зависеть от точности диаметра отверстия центрирующей втулки D. Погрешность закрепления EЗдля размера А1 равна нулю – это видно из схемы установки. Исходя из этого принимаем, что точность выполнения размера А1:
где погрешность базирования размера А1 равна:
В данной зависимости составляющие Smin и TD неизвестны. Решая равенство относительно их, получим:
По ГОСТ 25347-82 выбираем поле допуска отверстия так, чтобы соблюдалось условие Smin+TD≥ES
Из таблицы ГОСТ 25347-82 для размеров отверстий в интервале (80…120) мм находим:
При сравнении расчетной величины (Smin+TD)=0,036 с табличным значением верхнего отклонения отверстия (ES), видим, что условию (Smin+TD)≥ESудовлетворяют поля допусков отверстий G5(+0,017+0,012) и G6(+0,034+0,012) мм, которые могут быть приняты в качестве исполнительных размеров центрирующей втулки:
D=100G5 или D=100G6
Если базовая наружная цилиндрическая поверхность заготовки (d) выполнена с отклонениями поля допуска размера не основного вала, то предельные размеры центрирующей втулки (кольца) определяются (после выбора поля допуска отверстия) зависимостями:
Dmax=Dном+(es+ES),
Dmin=Dном+(es+EI)
На рисунке ниже приведена схема расположения полей допусков.
Базирование.
Назначение технологических баз.

При разработке технологического процесса огромное значение имеет назначение технологических баз. От правильности выбора технологических баз зависят производительность обработки, точность выполнения размеров, конструкция приспособлений, конструкция режущих и измерительных инструментов.
Исходными данными для назначения технологических баз являются:
сборочный чертеж изделия;
чертеж детали;
объем выпуска продукции;
наличие и состояние технологического оборудования;
оснащенность приспособлениями;
оснащенность режущим инструментом;
оснащенность измерительным инструментом;
квалификация рабочих.
При разработке технологической документации, технолог должен соблюдать принципы совмещения и постоянства баз.
Принцип совмещения баз.
Суть принципа совмещения состоит в том, что в качестве технологических баз следует назначать поверхности, которые одновременно являются конструкторскими и измерительными базами.
Основное преимущество данного принципа в том, что точность не зависит от размеров, получаемых при выполнении предыдущих операций. Однако часто расположение конструктивных элементов не позволяет выдержать принцип совмещения полностью, либо возникает необходимость применения сложной технологической оснастки на отдельных операциях.
Нарушение принципа совмещения баз приводит к удорожанию процесса обработки и снижению производительности. Если технологическая база не совпадает с конструкторской или измерительной, возникает необходимость замены размеров, заданных конструкторской документацией, более удобными технологическими размерами, проставленными от технологических баз. Это приводит к образованию технологических размерных цепей, и соответственно требуется ужесточение некоторых конструкторских размеров, отсюда удорожание процесса. Поэтому и нужно придерживаться принципа совмещения везде, где позволяет расположение конструктивных элементов.
Принцип постоянства баз.
При разработке и реализации технологического процесса необходимо стремиться к использованию одного и того же комплекта технологических баз на всех операциях изготовления изделия (детали).
Смена технологических баз по ходу технологического процесса приводит к увеличению длины технологических размерных цепей, увеличивая тем самым погрешности обработки.
При обработке сложных, многочисленных поверхностей, полностью обеспечить принципы совмещения и постоянства баз, практически невозможно. В любом случае при выборе установочных и направляющих баз предпочтение отдают конструктивным элементам с наибольшими габаритными размерами и точностью наложенных размерных связей.
На точность и экономичность установки, кроме размерной характеристики, оказывает влияние доступность конструктивных элементов, которые выполняют функцию баз. Само собой разумеется, что поверхность, открытая для контакта и сопряжения по всем координатным направлениям, будет наиболее удобна в качестве базы.
Также точность и удобство базирования зависят от формы базовых элементов. Приоритет конструктивных элементов при выборе баз следующий:
призматические (с плоскими поверхностями);
конические (с центрирующими и направляющими поверхностями);
цилиндрические (с направляющими и опорными поверхностями);
фасонные (со сложной конфигурацией).
Когда конструктивные элементы не могут служить базами, обеспечивающими требуемую точность установки, можно применять элементы, искусственно созданные исключительно для базирования. Самый яркий пример искусственных баз – центровые отверстия валов, создаваемые для их базирования при изготовлении.
Технологические базы бывают черновые и чистовые. Черновые базы являются необработанными и используются на первой операции технологического процесса. Отсюда следуют особые требования к этим базам:
черновые базы в связи со своей низкой точностью, должны использоваться только один раз на первой установке;
для обеспечения правильного взаимного положения обработанных и необработанных поверхностей в готовом изделии, черновыми базаминеобходимо назначать поверхности, которые в готовом изделии остаются черновыми.
Методика выбора технологических баз представлена на рисунке ниже.
Базирование.
Примеры задач по назначению технологических баз.

В данной статье рассмотрим несколько практических примеров по назначению технологических баз.
Пример №1.
Необходимо произвести выбор технологических баз заготовки, которые позволят обеспечить размеры А=60(+0,2-0,1) и а=10(+0,1-0,05) смотри рисунок ниже. Тип производства - мелкосерийное.
Чтобы обеспечить точность размера (а) настройкой режущего инструмента на этот размер, нужно использовать принцип совмещения баз. Однако использование данного принципа приводит к усложнению конструкции приспособления и значительному ухудшению условий обработки. Для мелкосерийного производства это нежелательно.
Давайте рассмотрим базирование заготовки по другой схеме. В качестве технологической базы будем использовать плоскость 1, которая не совпадает с измерительной базой 2.
При данной схеме базирования, на настроенном станке размеры n и b будут постоянны. Следовательно размер глубины паза (а) не может быть выдержан точно, так как на его колебания будет влиять погрешность размера А, выдерживаемого на предыдущей операции. Нам нужно, на операции фрезерование паза, для обеспечения размера (а) рассчитать размер (b) и допуск на него. Технологический размер (b) рассчитывается, исходя из размерной цепи. В указанной цепи размер (а)является замыкающим, так как именно для него необходимо выдержать точность.
Из уравнения размерной цепи получаем, для номинальных размеров:
а=А-b; b=А-а=60-10=50 мм
Для допусков:
Ta=TА+Tb; Tb=Ta-TА=0,15-0,3=-0,15 мм
По результатам расчета мы получили отрицательный допуск. Такого быть не может, поскольку, допуск всегда является положительной величиной. В связи с этим можно сделать вывод о том, что размер (a) невозможно обеспечить в заданных условиях. Говоря другими словами, принятая схема базирования на этой операции не позволяет решить поставленную задачу.
Чтобы решить задачу для данной схемы базирования, необходимо ужесточить допуск размера А. Он устанавливается равным половине допуска на размер замыкающего звена (в нашем примере 015/2≈0,08). Устанавливаем допуск на размер:
А=60+0,04-0,04, т.е. Tа=0,08 мм
Тогда допуск размера b равен:
Tb=Ta-TА=0,15-0,08=0,07 мм
Теперь определим расположение поля допуска Tb относительно номинального размера b расчетом размерной цепи на максимум и минимум:
аmax=Аmax-bmin ;
аmin=Аmin-bmax ;
откуда:
bmin=Аmax-amax=60,04-10,1=49,94 мм ;
bmax=Аmin-amin=59,96-9,95=50,01 мм ;
Мы получили искомый технологический размер (b=50+0,1-0,06) , его и будем указывать на эскизе обработки к данной операции.
Пример №2.
На токарном станке необходимо полностью обработать деталь шкив, обеспечивая параллельность торцов 1,2 и перпендикулярность их к оси А – А. Кроме того необходимо обеспечить концентричность поверхностей 3 и 4.Заготовка – отливка из серого чугуна. Нам нужно определить технологические базы и содержание токарной операции. Эскиз заготовки представлен на рисунке ниже.
Проанализируем два варианта обработки.
Вариант 1.
Выберем наружную цилиндрическую поверхность 4 и торец 1 в качестве черновых технологических баз. От выбранных баз на токарном станке в трехкулачковом самоцентрирующем патроне производятся следующие переходы: подрезка торца 2 и расточка отверстия в ступице, тем самым обеспечивается перпендикулярность торца2 к оси А – А.
Во втором установе, комплектом чистовых технологических баз будет обработанный торец 2 и отверстие 3. На специальной оправке подрезается торец 1 и обтачивается поверхность 4. В результате этой операции обеспечивается параллельность торцов 1 и 2 и перпендикулярность их к оси А – А, кроме того обеспечивается концентричность поверхностей 3 и 4. Казалось бы поставленная задача решена, но это не так. Мы обеспечили точное расположение всех обработанных поверхностей, а положение необработанных поверхностей относительно обработанных осталось неучтенным. Визуально обработанный таким образом шкив можно определить по разностенности обода шкива и по эксцентрическому положению отверстия 3 в ступице.
Вариант 2.
Для этого варианта в качестве черновых технологических баз выбирается внутренняя поверхность 5 обода и внутренний торец 6. Такая схема базирования (смотри рисунок ниже), обеспечит минимальный эксцентриситет наружной поверхности относительно внутренней, а также достаточно точно толщину обода.
В данном случае обработка шкива осуществляется за один установ. В связи с этим все технические требования выполняются, и комплект необработанных поверхностей занимает определенное положение относительно обработанных.