Министерство образования Нижегородской области
ГОУ СПО «Саровский политехнический техникум»
Расчет сил зажима и силового привода
при проектировании станочных приспособлений
Методические указания к выполнению практических работ и разделов в курсовых и дипломных проектах для студентов специальности: «Технология машиностроения»
Саров 2008
Министерство образования Нижегородской области
ГОУ СПО «Саровский политехнический техникум»
Расчет сил зажима и силового привода
при проектировании станочных приспособлений
Методические указания к выполнению практических работ и разделов в курсовых и дипломных проектах для студентов специальности: 151001 Технология машиностроения
Составила: Суняйкина Н.Н. –
преподаватель высшей категории
специальных дисциплин ГОУ СПО СПТ
Рецензенты: Дуганова Л.А. –
преподаватель специальных дисциплин
ГОУ СПО СПТ
Иванов А.А. –
к.т.н., преподаватель ФГОУ ВПО
«Саровского государственного физико-
технического института»
Настоящие методические указания обобщают теоретические и практические вопросы по теме «Расчет сил зажима и силового привода» при проектировании технологической оснастки для металлообрабатывающих станков, даны характеристики пневматическим приводам, их недостатки и преимущества, рассмотрены основные этапы проведения расчетов в практических работах и разделах курсовых и дипломных проектов по проектированию технологической оснастки. Комплексно изложен порядок выполнения расчетов и приведен пример расчетов.
Пособие предназначено для студентов специальности 151001 «Технология машиностроения» начального, среднего и высшего профессионального образования, а также для руководителей курсовых и дипломных проектов.
Согласовано заседанием выпускной ПЦК ГОУ СПО СПТ
Протокол № ___ от “____” _____________20 г
Утверждено заседанием методического совета ГОУ СПО СПТ
Протокол № ___ от “____” _____________20 г
ОГЛАВЛЕНИЕ
1. Расчет сил зажима………………………..…………..............................…. 4
2. Расчет силового привода………………………………………………..... 21
3. Примеры расчетов…………………………………………………………. 26
В пособии использованы источники:
1. Антонюк В.Е. В помощь молодому конструктору станочных приспособлений. – Минск.: Машиностроение, 1975.
2. Справочник технолога – машиностроителя. Том 2.Под ред. А.Г.Косиловой и Р.К.Мещерякова.-4-е изд.,перераб. и доп. – М.: Машиностроение, 1985.
1 Расчет сил зажима
Обрабатываемая деталь находится в равновесии как под действием сил, возникающих в процессе обработки, так и сил зажима и реакций опор. Основными силами процесса обработки являются силы резания. При расчете сил зажима реже учитываются силы веса, центробежные и инерционные, возникающие при определенных условиях обработки.
Величина сил зажима определяется из условия равновесия всех перечисленных сил при полном сохранении контакта базовых поверхностей обрабатываемой детали с установочными элементами приспособления и исключении возможности сдвига в процессе обработки. При расчетах следует ориентироваться на такие величину, место приложения и направление сил зажима, при которых силы зажима получаются наибольшими. Определять требуемую силу зажима нужно с учетом коэффициента запаса К, предусматривающего возможное увеличение силы резания вследствие затупления режущего инструмента, неоднородности обрабатываемого металла, неравномерности припуска, непостоянства установки, закрепления заготовки и т. д.
а) при зажиме не должно нарушаться заданное положение детали;
б) зажимы не должны вызывать деформации деталей и порчи их поверхностей;
в) закрепление и открепление детали должно производиться с минимальной затратой сил и времени рабочего;
г) силы резания по возможности не должны восприниматься зажимными устройствами;
д) при закреплении недостаточно жестких деталей силы зажима должны располагаться над опорами или близко к ним.
а) место приложения и направления сил зажима;
б) величина сил резания и их моменты, действующие на обрабатываемую деталь, а при необходимости инерционные и центробежные силы, возникающие при обработке;
в) величина усилий зажима при решении задачи статики на равновесие твердого тела, находящегося под действием всех приложенных к нему сил;
г) требуемая величина сил зажима путем умножения найденного значения сил зажима на коэффициент запаса К.
Коэффициент К рассчитывается применительно к конкретным условиям обработки по формуле:
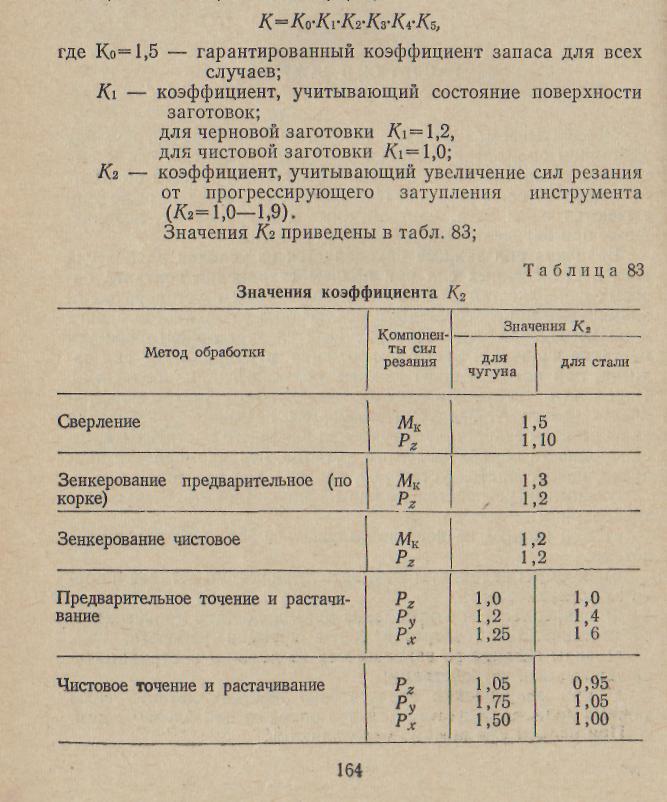
Таблицы 83 – 89 Антонюк В.Е. В помощь молодому конструктору станочных приспособлений. . – Минск.: Машиностроение, 1975.
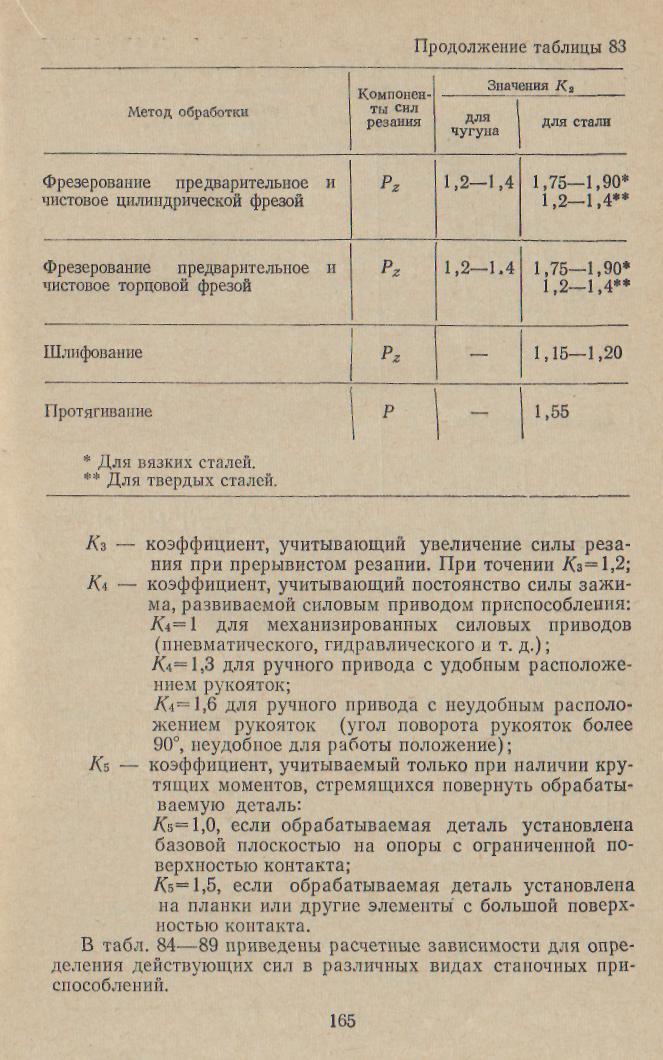

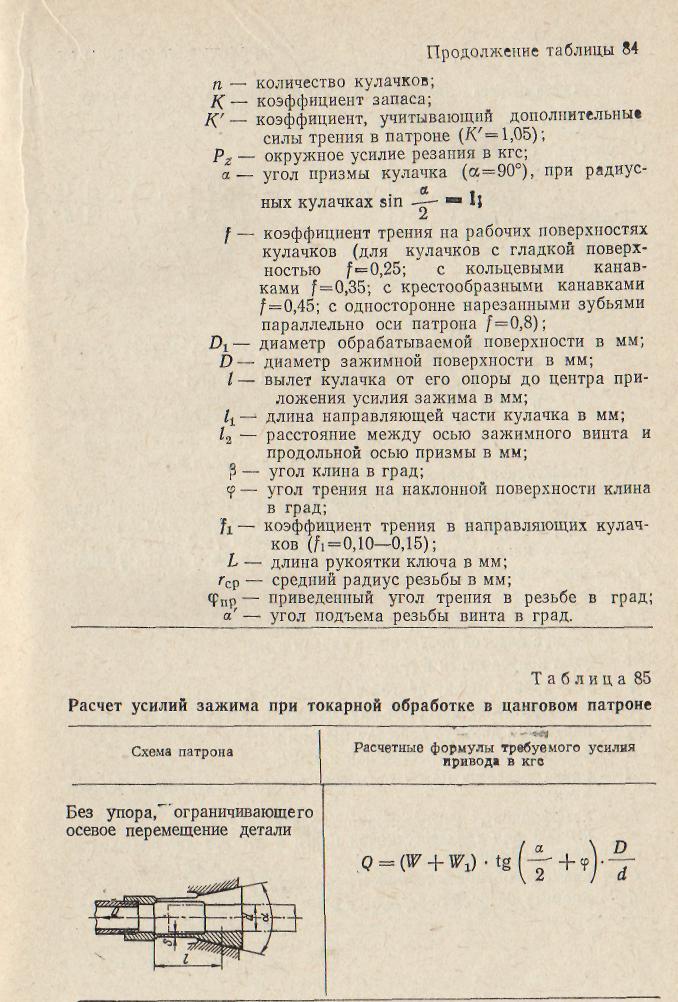
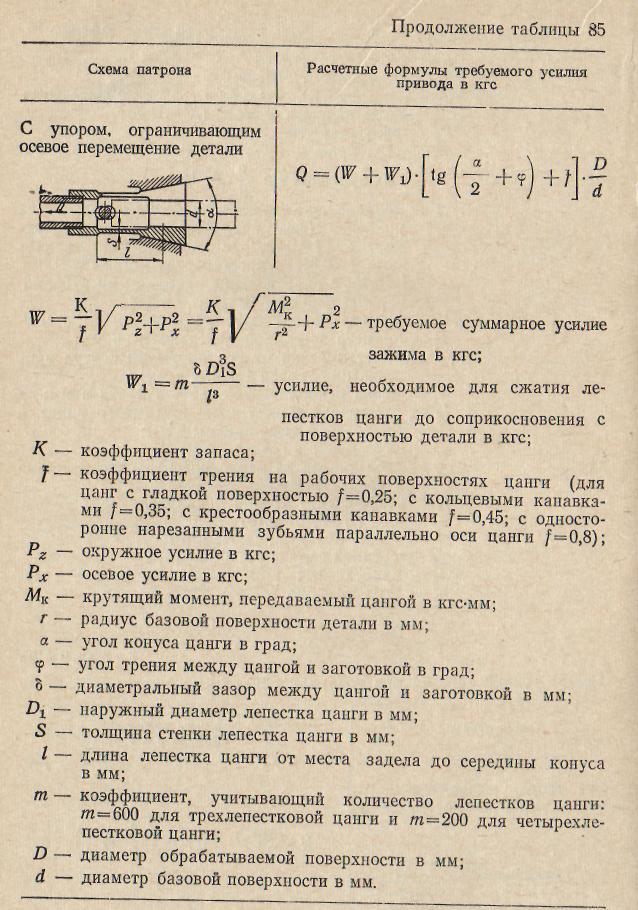
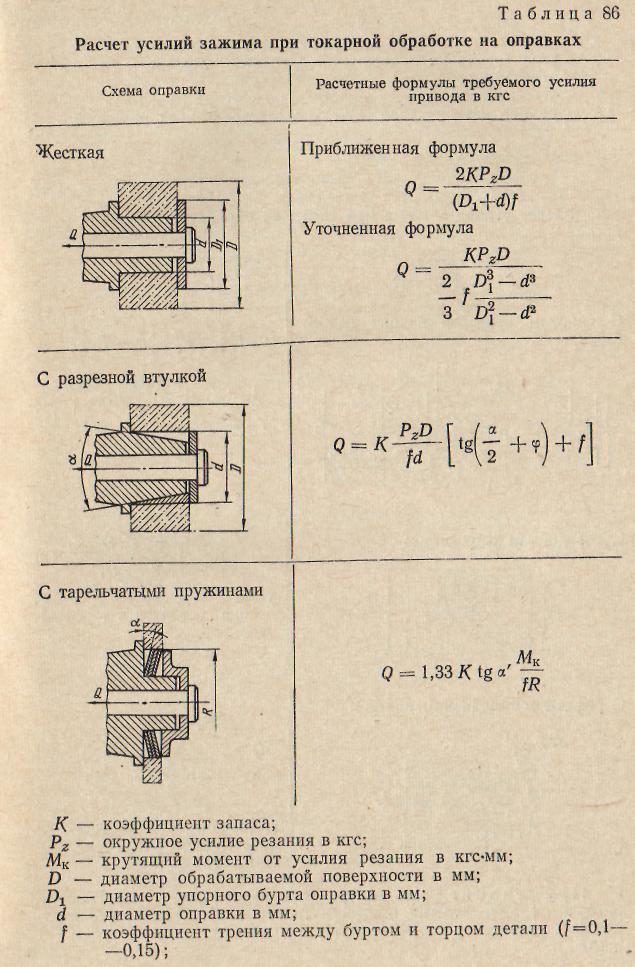
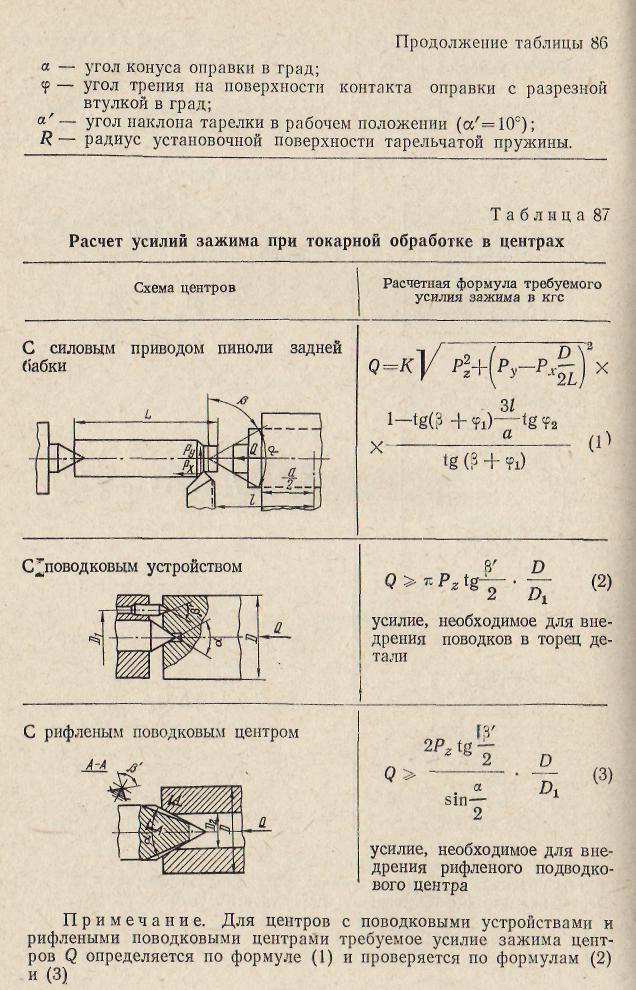
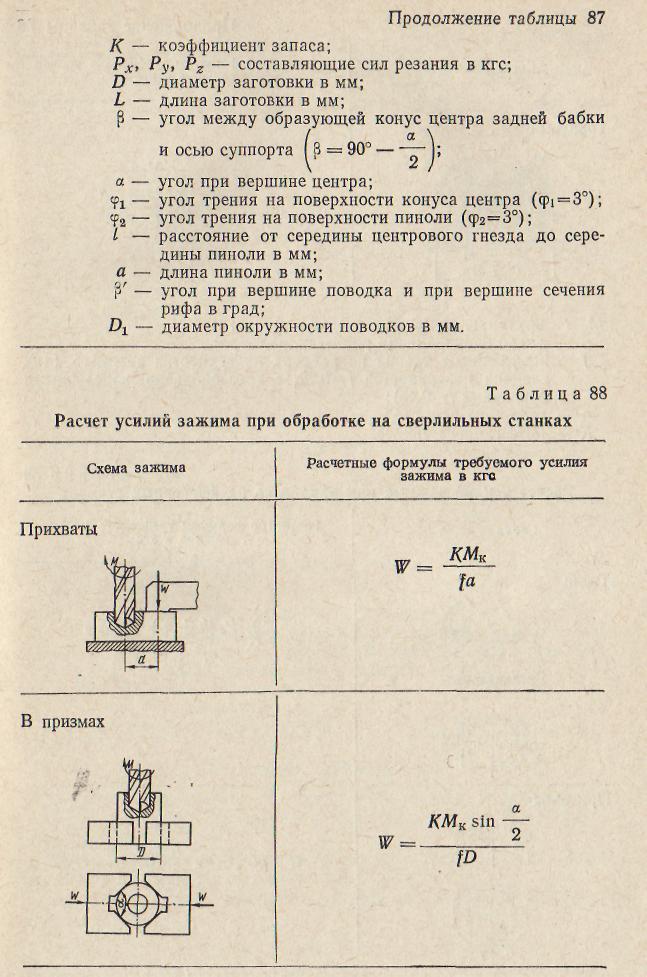
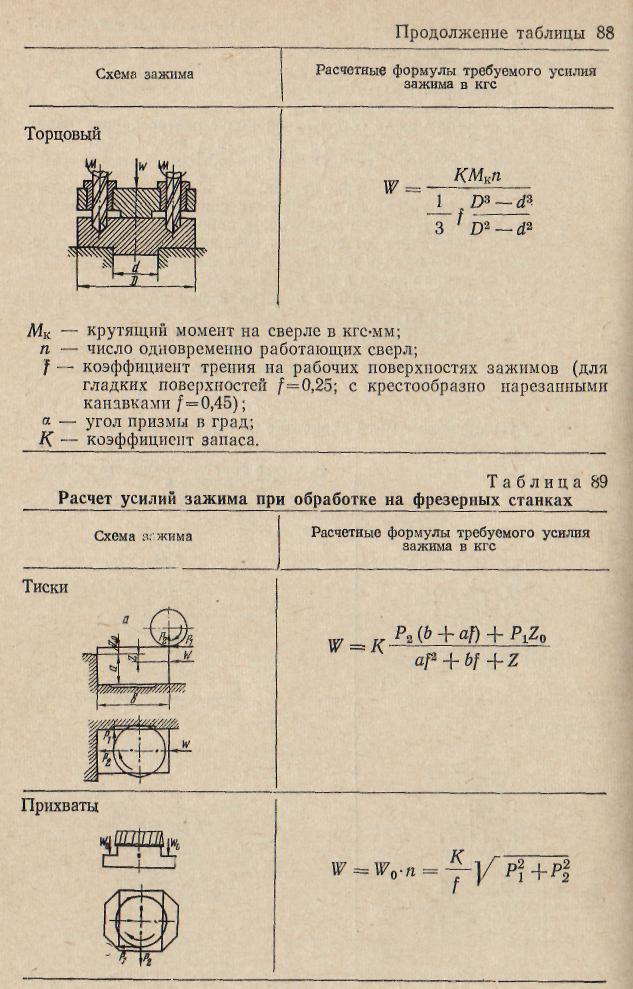
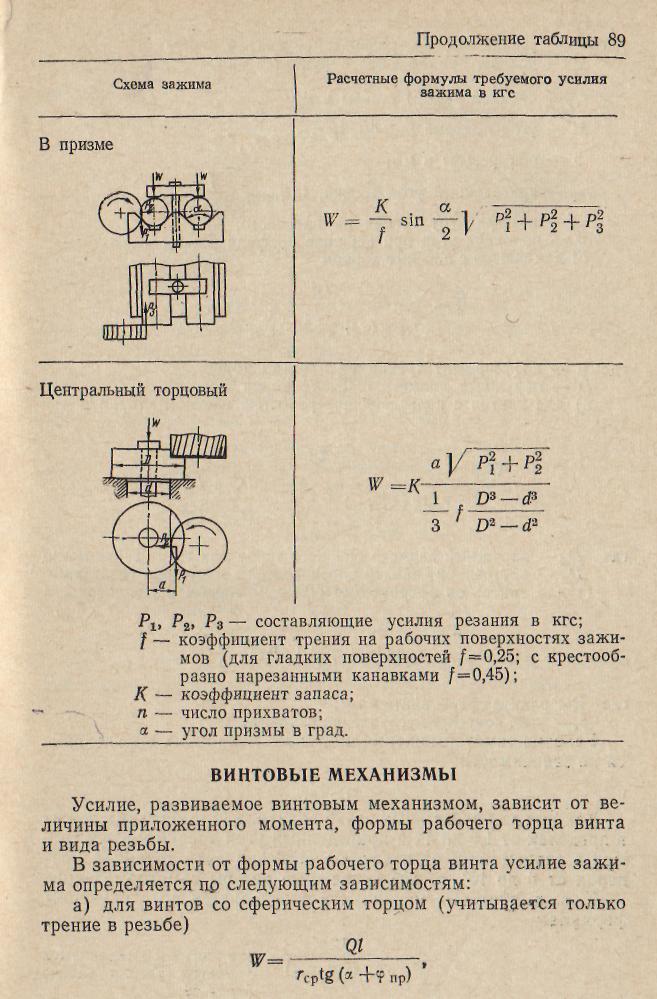
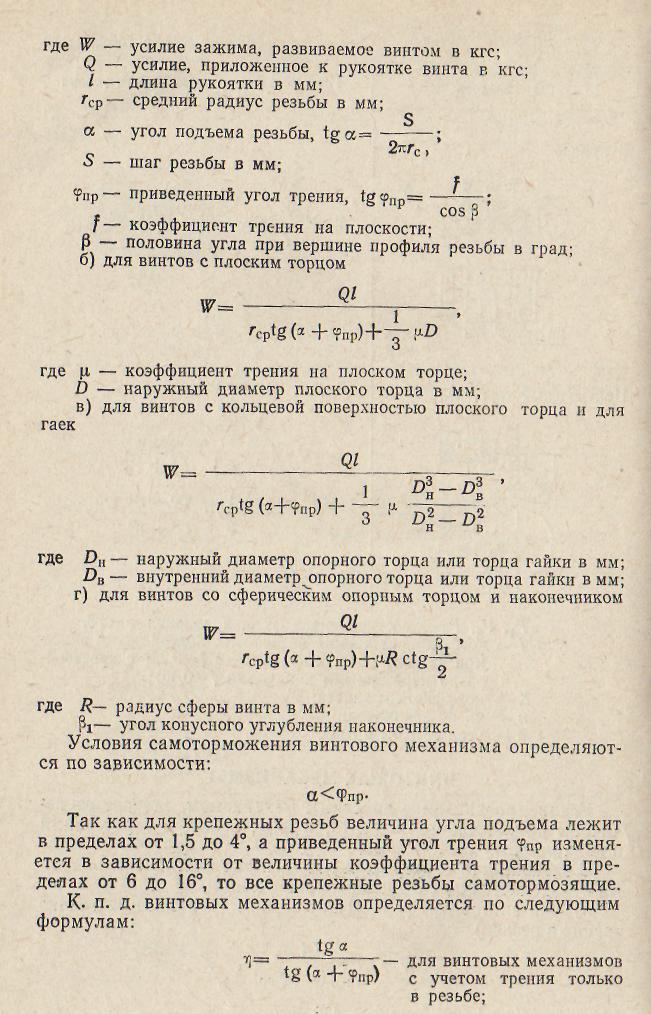
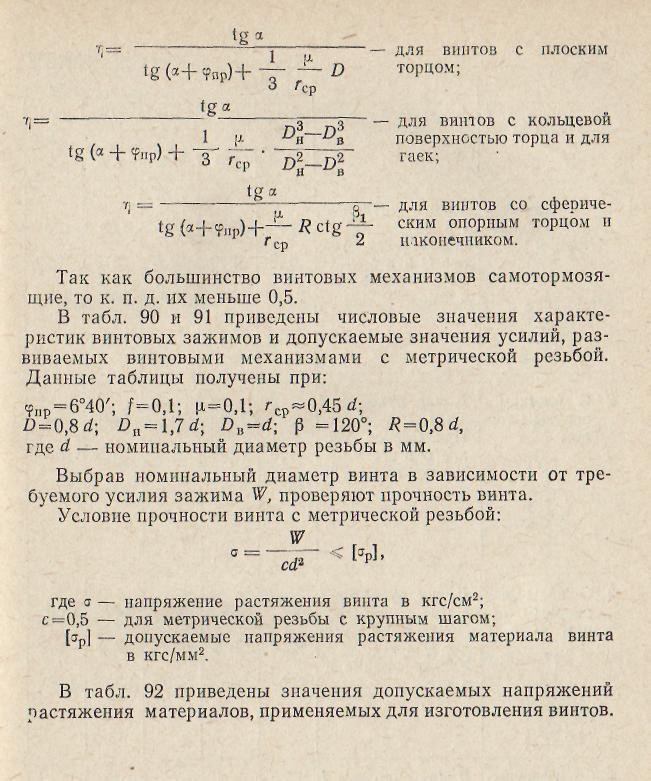
Таблицы 8, 10, 17 Справочник технолога – машиностроителя. Том 2.Под редакцией А.Г.Косиловой и Р.К.Мещерякова.-4-е изд.,перераб. и доп. – М.: Машиностроение, 2001.

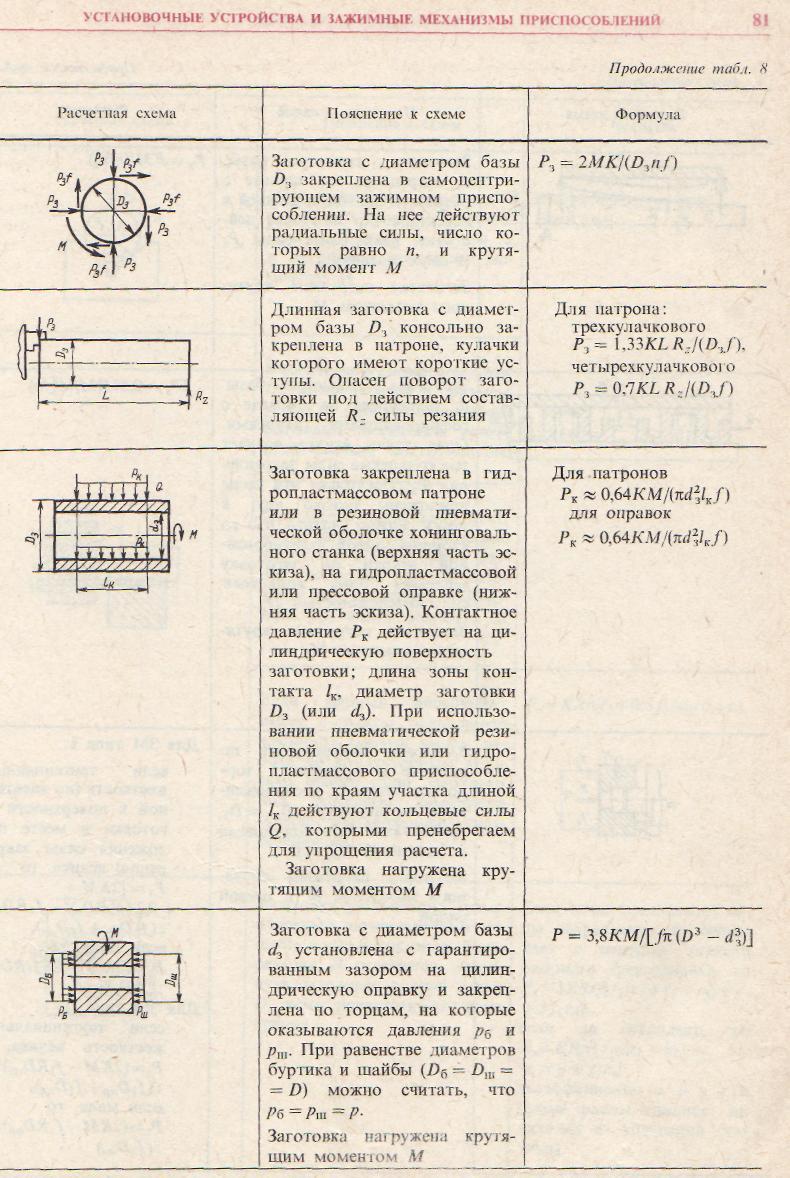
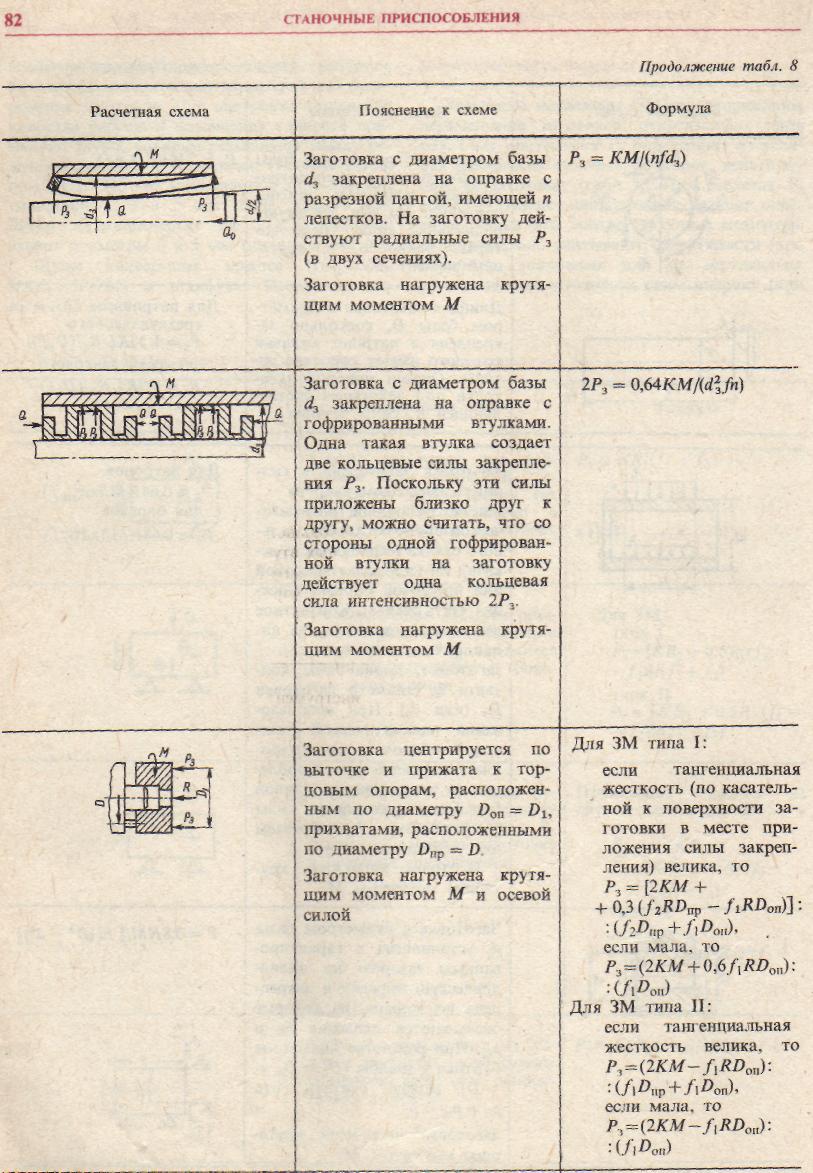
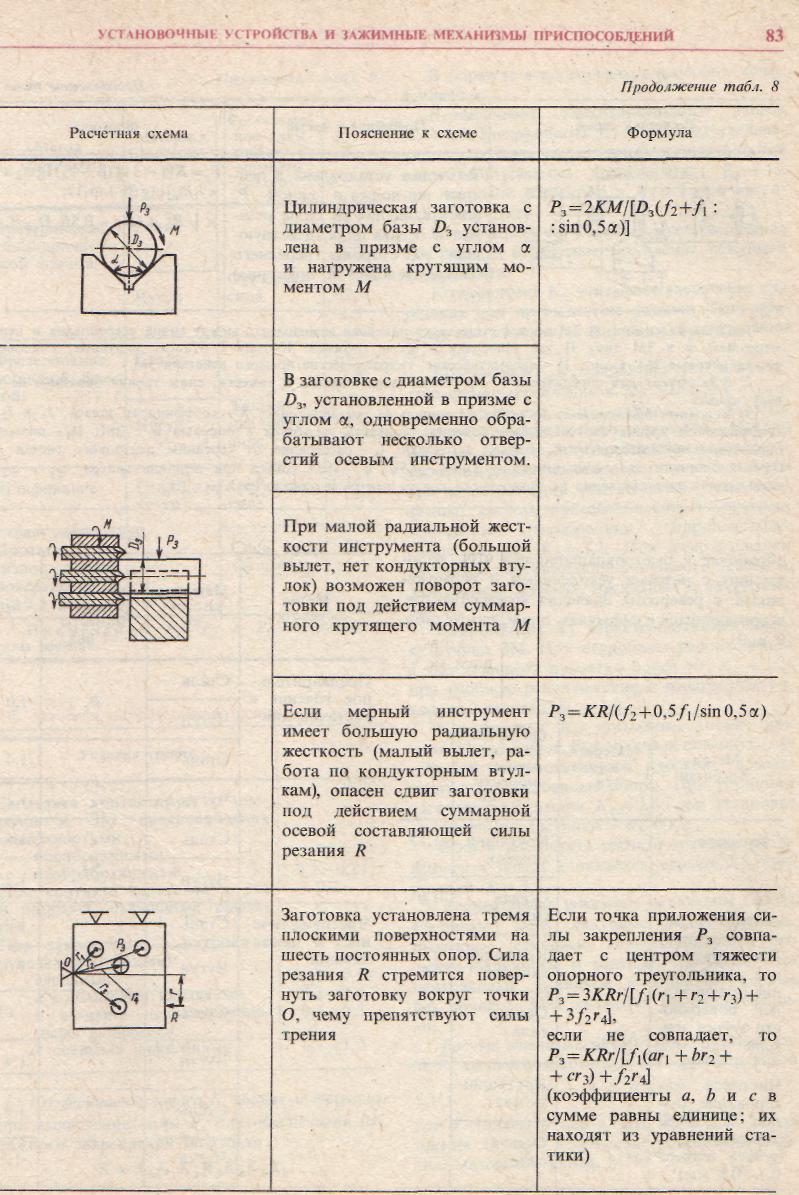
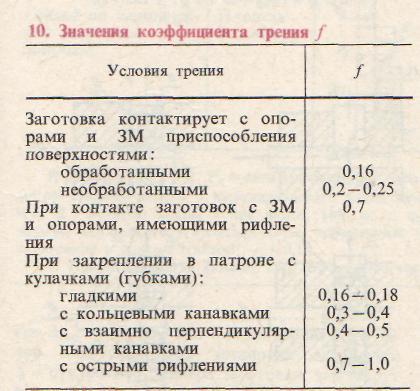
2 Расчет силового привода
В массовом и серийном производстве наибольшее применение получили пневматические приводы. Это объясняется тем, что пневматические приводы приспособлений имеют простую конструкцию, являются быстродействующими, просты в управлении, обладают надежностью и сравнительно недорого стоят. Общие технические требования на пневмоприводы даны в ГОСТ 18460—73.
Силовые пневматические приводы состоят из пневмодвигателей, пневматической аппаратуры и воздухопроводов.
Пневматические силовые приводы разделяют по виду пневмодвигателя на пневматические цилиндры с поршнем и пневматические камеры с диафрагмами.
По способу компоновки с приспособлениями поршневые и диафрагменные пневмоприводы разделяют на встроенные, прикрепляемые и универсальные. Встроенные пневмоприводы размещают в корпусе приспособления и составляют с ним одно целое. Прикрепляемые пневмоприводы устанавливают на корпусе приспособления, соединяют с зажимными устройствами, их можно отсоединять от него и применять на других приспособлениях. Универсальный (приставной) пневмопривод — это специальный пневмоагрегат, применяемый для перемещения зажимных устройств в различных станочных приспособлениях.
Пневматические поршневые и диафрагменные пневмодвигатели бывают одно- и двустороннего действия. В пневмодвигателях одностороннего действия рабочий ход поршня со штоком в пневмоцилиндре или прогиб диафрагмы в пневмокамере производится сжатым воздухом, а обратный ход поршня со штоком или диафрагмы со штоком — под действием пружины, установленной на штоке. Пневмоприводы одностороннего действия применяют в тех случаях, когда при зажиме детали требуется сила, большая, чем при разжиме; пневмоприводы двустороннего действия — когда при зажиме и разжиме детали в приспособлении требуется большая сила, например в приспособлениях с самотормозящимися зажимными устройствами.
Пневмоприводы по виду установки делятся на невращающиеся и вращающиеся. Невращающиеся пневмоприводы применяют в стационарных приспособлениях, устанавливаемых на столах сверлильных и фрезерных станков, вращающиеся пневмоприводы — для перемещения зажимных устройств вращающихся приспособлений (патроны токарных станков). Пневмоприводы применяют также для зажимных устройств приспособлений, устанавливаемых на непрерывно или периодически вращающихся круглых столах станков.
Замена в станочных приспособлениях ручных зажимов механизированными (пневматическими) дает большие преимущества:
1) значительное сокращение времени на зажим и разжим обрабатываемых деталей (в 4—8 раз) вследствие быстроты действия (0,5—1,2 с) пневмопривода;
2) постоянство силы зажима детали в приспособлении;
3) возможность регулирования силы зажима детали;
4) простота управления зажимными устройствами приспособлений;
5) бесперебойность работы пневмопривода при изменениях температуры воздуха в цехе.
Недостатки пневматического привода:
1) нестабильная плавность перемещения рабочих элементов из-за сжимаемости воздуха, особенно при переменной нагрузке;
2) небольшое давление сжатого воздуха в полостях пневмоцилиндра и пневмокамеры (0,39 – 0,49 МПа (4—5 кгс/см2);
3) относительно большие размеры пневмоприводов для получения значительных сил на штоке пневмопривода.
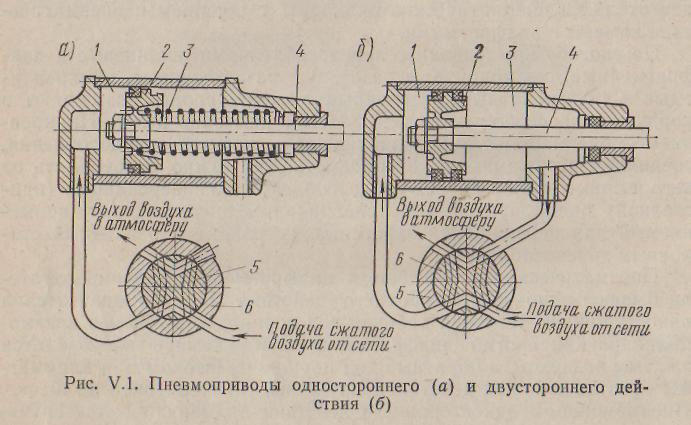
Пневматические поршневые приводы.
В поршневых пневмоприводах одностороннего действия (рис. V.1, а) сжатый воздух подается только в одну полость 1 пневмоцилиндра и перемещает поршень 2 со штоком 4 вправо при зажиме детали. При разжиме детали поршень 2 со штоком 4 отводится влево пружиной 3, установленной на штоке, а воздух через золотник 5 крана 6 уходит в атмосферу.
В поршневых пневмоприводах двустороннего действия (рис. V.1, б) сжатый воздух поочередно подается в полости 1 и 3 пневмоцилиндра и перемещает поршень 2 со штоком 4 при зажиме и разжиме деталей. Золотник 6 распределительного крана 5 при повороте рукоятки производит последовательную подачу сжатого воздуха в полость 1 или 3 пневмоцилиндра и выпуск воздуха из полостей 1 или 3 в атмосферу.
При расчете пневмоприводов определяют осевую силу на штоке поршня, зависящую от диаметра пневмоцилиндра и давления сжатого воздуха в его полостях. Можно по заданной силе на штоке поршня и давлению сжатого воздуха определить диаметр пневмоцилиндра. В приспособлениях с пневмоприводом следует определять время его срабатывания.
Расчет осевой силы Q на штоке поршневого привода производится по следующим формулам:
;
;
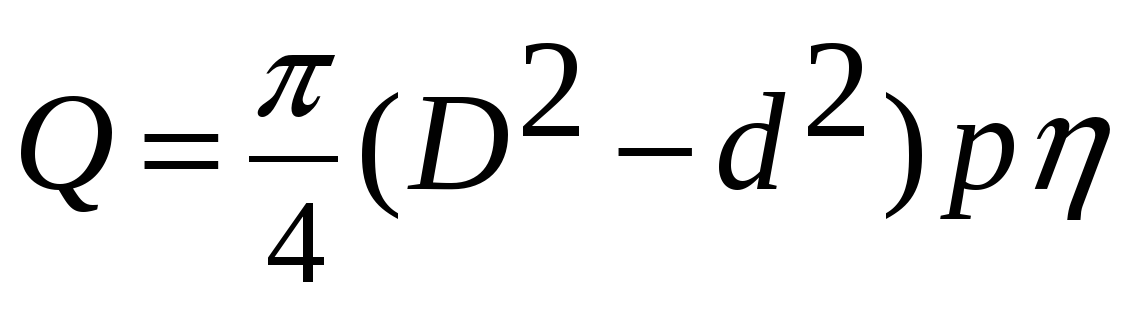
где D – диаметр пневмоцилиндра (поршня), см;
d — диаметр штока поршня, см;
р = 0,40 —давление сжатого воздуха, МПа (р = 4 кгс/см2);
η = 0,85—0,9 КПД, учитывающий потери в пневмоцилиндре;
Q1 – сила сопротивления возвратной пружины в конце рабочего хода поршня, Н (кгс).
Возвратная пружина на штоке при ее предельном сжатии (в конце рабочего хода поршня) должна оказывать сопротивление от 5% при больших до 20% при малых диаметрах пневмоцилиндра от силы Q на штоке пневмоцилиндра в момент зажима детали в приспособлении.
Практически применяют следующие размеры диаметров D рабочей полости цилиндров: 75, 100, 125, 200, 250, 300, 350 мм._
Определяют диаметр пневмоцилиндра двустороннего действия по заданной силе Q и давлению сжатого воздуха р.
В формуле
для упрощения расчета опускается КПД, но для надежности зажима найденную силу Q на штоке увеличивают в 1,5 раза. Тогда формула для Q примет вид
,
откуда
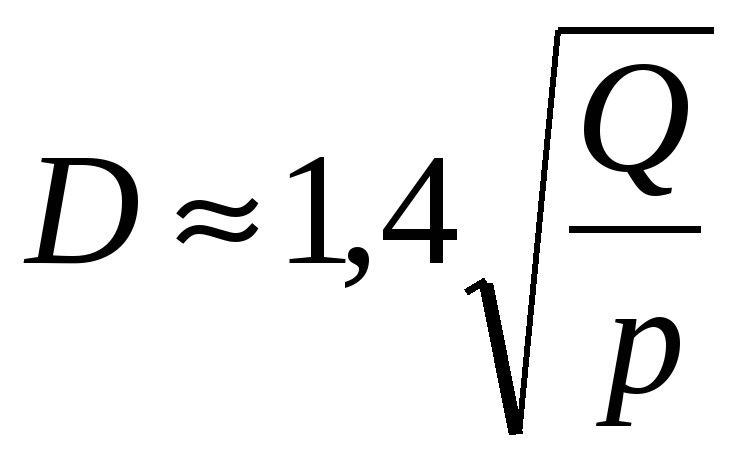
Принимая р = 0,4 МПа (4 кгс/см2), находится диаметр пневмоцилиндра:
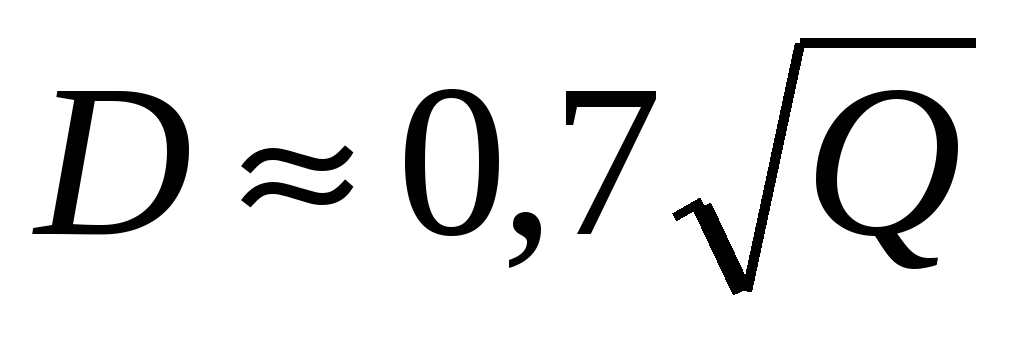
Найденный размер диаметра пневмоцилиндра округляют по нормали (таблица 107, таблица 17) и по принятому диаметру определяют действительную осевую силу Q на штоке по вышеперечисленным формулам.
3 Примеры расчетов
3.1 Составление схемы базирования заготовки на операции
Специальное станочное приспособление разрабатывается на сверлильную.
По заданию необходимо сверлить четыре отверстия диаметром 6,8 Н12 мм под резьбу М8-7Н мм.
В качестве инструмента выбирается спиральное сверло с коническим хвостовиком, из быстрорежущей стали Р6М5, диаметром 6,8 h9() мм, которое обеспечивает 12 квалитет точности.
Выбор технологических баз во многом определяет точность изготовления детали и экономичность ее изготовления.
Деталь “планшайба” базируется по типовой схеме базирования диска (рисунок 1):

Рисунок 1 - Схема базирования детали
- установочная база, лишает заготовку трех степеней свободы (опорные точки 1, 2, 3, технологическая, явная);
- двойная опорная, лишает заготовку двух степеней свободы (опорные точки 4, 5, технологическая, явная);
- опорная база, лишает заготовку одной степени свободы (опорная точка 6, технологическая, явная).
3.2 Выбор варианта приспособления
Для обработки отверстий на станках сверлильной группы проектируется и изготавливается различная оснастка: кондукторы, поворотные столы и стойки, многошпиндельные и револьверные головки, всевозможные вспомогательные инструменты и т.д.
Основное приспособление, применяемое на сверлильных станках – кондуктор.
В общем случае приспособление кондуктор состоит из следующих основных элементов: установочного (базирующего), который определяет положение заготовки в процессе обработки; зажимного, осуществляющего закрепление и освобождение заготовки; направляющего, служащего для правильной ориентации инструмента в процессе обработки. Все узлы монтируются в корпус приспособления.
Закрепление заготовки можно производить с использованием винтовых, эксцентриковых зажимов, а так же с помощью механизированного зажима.
Так как заданием предусмотрено, что производство крупносерийное, то выбирается кондуктор с пневматическим приводом, потому что он обладает следующими преимуществами перед другими приводами:
- обладает значительным быстродействием (0,5-1,2 с), что значительно сокращает время зажима и разжима детали;
- постоянство силы зажима;
- бесперебойность работы при изменении температуры воздуха окружающей среды в широком диапазоне;
- освобождение от приемов по управлению зажимов;
- относительная дешевизна конструкции.
3.3 Составление расчетной схемы приспособления
Расчетная схема приспособления – это схема, на которой изображаются все усилия, действующие на заготовку: сила резания, крутящий момент, зажимное усилие. Расчетная схема приспособления приведена на рисунке 2.
Рисунок 2 – Расчетная схема приспособления
Конструктивная схема приспособления – это упрощенное изображение приспособления, с его основными элементами. Данная схема представлена на рисунке 3.
3.4 Расчет сил зажима
Приложенные к заготовке силы должны предотвратить возможный отрыв заготовки, сдвиг или поворот ее под действием сил резания и обеспечить надежное закрепление заготовки в течение всего времени обработки.
Сила зажима заготовки при данном способе закрепления определяется по следующей формуле:
(1)
где М - крутящий момент при сверлении, М= 4,7 Н м;
- коэффициент трения на рабочей поверхности зажима, = 0,1;

Рисунок 3 – Конструктивная схема приспособления
а – расстояние от точки приложения силы до осевой линии обрабатываемого отверстия, а = 91,25 мм;
К – коэффициент запаса, который определяют по формуле:
(2)
где - гарантированный коэффициент запаса, =1,5;
- поправочный коэффициент, учитывающий вид поверхности детали, К= 1;
- поправочный коэффициент, учитывающий увеличение силы резания при затуплении режущего инструмента, К= 1,4;
- поправочный коэффициент, учитывающий увеличение силы резания при обработке прерывистых поверхностей детали (в данном случае отсутствует);
К- поправочный коэффициент, учитывающий непостоянство силы зажима, развиваемой силовым приводом приспособления, К= 1;
К- поправочный коэффициент, учитывающий степень удобства расположения рукоятки в ручных зажимных устройствах (в данном случае отсутствует);
К- поправочный коэффициент, учитывающий неопределенность места контакта заготовки с опорными элементами, имеющими большую опорную поверхность, К= 1,5.
Так как значение коэффициента К больше 2,5, то принимается полученное значение 3,15.
.
3.5 Расчет силового привода
Так как зажим заготовки осуществляется без промежуточного звена, то усилие на штоке будет равно силе зажима заготовки, то есть
Диаметр пневмоцилиндра двух стороннего действия при подаче воздуха со стороны штока, определяется по следующей формуле:
(3)
где р – давление сжатого воздуха, р = 0,4 МПа;
η – КПД, η =0,8;
d – диаметр штока.
d = 0,4D. (4)
(5)
Диаметр пневмоцилиндра принимается равным 100 мм.
Диаметр штока будет равен
d = 0,4100 = 40 мм.
Действительное усилие на штоке:
(6)
29